Elementy z tworzyw termoplastycznych wykonane metodą wtryskiwania stosowane są bardzo szeroko w różnych gałęziach przemysłu z uwagi na łatwość i szybkość wytwarzania skomplikowanych kształtów. Pozwala to na dużą swobodę na etapie projektowania elementu, jednocześnie umożliwiając obniżenie kosztów jego produkcji.
W ostatnich latach popularne stało się także wprowadzanie termoplastów do produkcji elementów konstrukcyjnych, wykonywanych dotychczas najczęściej z metali, bądź innych materiałów charakteryzujących się wysoką wytrzymałością mechaniczną. W tego typu aplikacjach stosowane są techniczne kompozyty termoplastyczne, których własności mechaniczne podniesione są dzięki zastosowaniu wypełniaczy, najczęściej w postaci włókien szklanych. Zastosowanie włókien powoduje, iż izotropowy materiał osnowy termoplastycznej zamienia się w anizotropowy kompozyt o dużej zmienności własności, w zależności od kierunku orientacji znajdujących się w nim włókien. Orientacja włókien jest zależna od kierunku płynięcia tworzywa w gnieździe formy podczas procesu wtryskiwania. Z uwagi na trudność predykcji orientacji, a co za tym idzie jej wpływu na własności kompozytu, opisywana anizotropia jest często pomijana na etapie projektowania detali. Czasami inżynierowie stosują uproszczone podejścia mające oszacować jej wpływ na sztywność i wytrzymałość materiału, jednak w obydwu przypadkach może to prowadzić do projektu zbyt słabego bądź też przewymiarowanego elementu. Pomocne stają się tutaj wyniki obliczeń numerycznych pozwalające na wyznaczenie wpływu procesu wtryskiwania na własności mechaniczne końcowego produktu.
Orientacja włókien a własności mechaniczne kompozytów termoplastycznych
Podstawowym źródłem informacji na temat własności kompozytów termoplastycznych są ich karty techniczne. Podstawowe własności mechaniczne zawarte w tych kartach wyznaczane są w oparciu o wyniki próby rozciągania wg normy ISO 527. Próbki do testów rozciągania wykonywane zgodnie z tą normą mają kształt wiosełek, kształtowanych bezpośrednio w procesie wtryskiwania. Z uwagi na jednokierunkowy przepływ materiału w gnieździe formy, wynikający z kształtu wiosełka, uzyskiwane próbki charakteryzują się wysokim stopniem orientacji włókien w kierunku działania siły podczas próby rozciągania. Stopień zorientowania włókien w tak wytworzonym wiosełku zazwyczaj mieści się w przedziale od 80 do 90%.
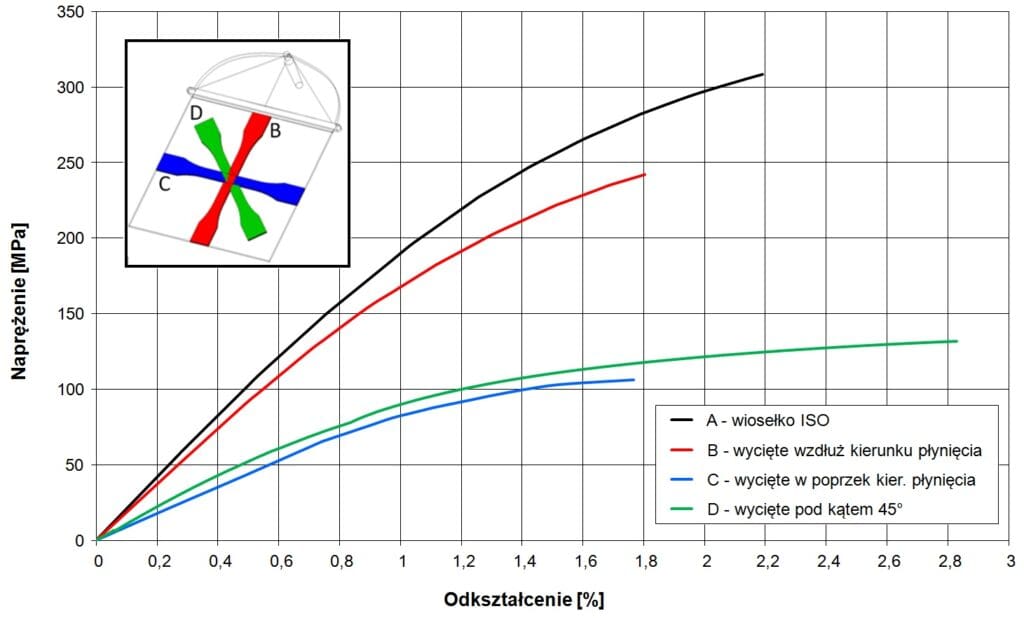
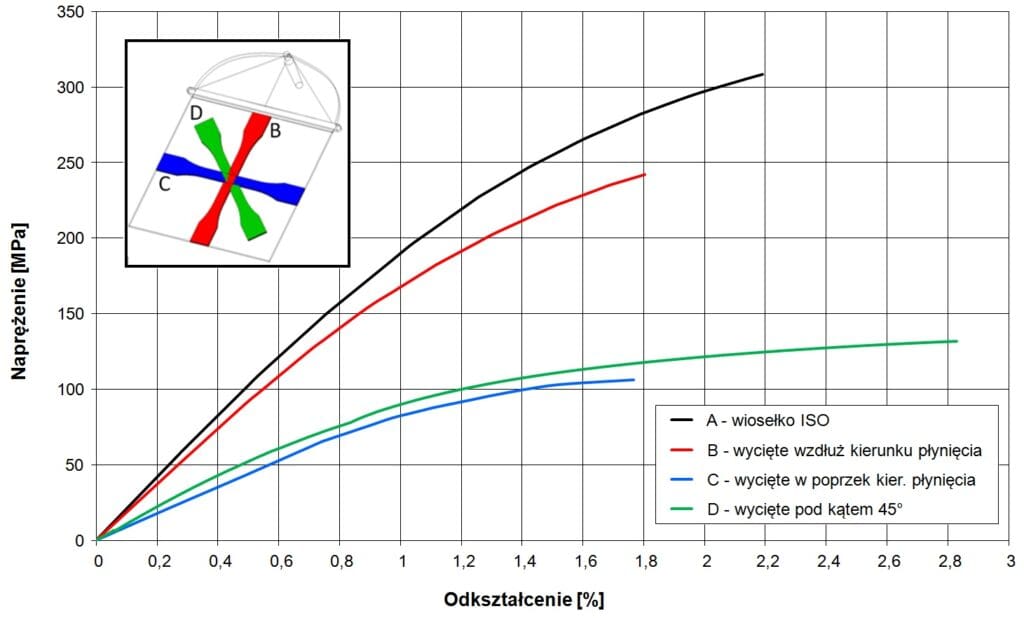
W celu wyznaczenia wpływu orientacji na własności mechaniczne materiału przygotowano wiosełka o kształcie zgodnym z wymienioną normą, jednak charakteryzujące się różną orientacją włókien. Wiosełka te wycinane były strumieniem wody pod różnymi kątami z płytki kwadratowej o jednokierunkowej orientacji. Na rysunku 1 przedstawiono kierunki wycięcia wiosełek z płytki oraz porównanie wyników ich rozciągania odniesione do wiosełka referencyjnego wtryskiwanego wg normy ISO 527. Wszystkie próbki wykonane były z materiału z grupy poliamidów, wypełnionego w 50% włóknem szklanym. Jak widać na przedstawionym wykresie, nawet w przypadku wiosełka wycinanego z płytki w kierunku płynięcia materiału, a więc – orientacji włókien (próbka B), wytrzymałość do zerwania jest o około 20% niższa niż dla wiosełka wtryskiwanego bezpośrednio wg ISO 527 (próbka A). Tym samym wytrzymałość materiału wtryskiwanej płytki, przy obciążeniu w tym kierunku, jest o 20% niższa w stosunku do wartości, jaka znajduje się w karcie technicznej materiału. W przypadku badania wytrzymałości w kierunku poprzecznym do kierunku płynięcia materiału (próbka C) wiosełko ulega zniszczeniu przy osiągnięciu zaledwie 40% wytrzymałości podanej przez producenta materiału w jego karcie. Równie niską wytrzymałością charakteryzowało się wiosełko wycięte pod kątem 45° do kierunku płynięcia tworzywa (próbka D).
Podstawowym wnioskiem wynikającym z analizy powyższych wyników jest fakt, iż własności wytrzymałościowe mierzone w kierunku największej sztywności są zawyżone w stosunku do własności materiału we wtryskiwanym produkcie końcowym. Przedstawione wyniki w sposób jednoznaczny wskazują na konieczność uwzględniania orientacji włókien podczas projektowania detali wykonanych z kompozytów termoplastycznych. Tak duża zmienność wytrzymałości lokalnej materiału musi zostać uwzględniona podczas interpretacji wartości naprężeń występujących w elemencie pod wpływem działania sił zewnętrznych. W zależności od lokalnej orientacji materiału mogą one stanowić o przekroczeniu (lub też o nie przekroczeniu) nośności granicznej materiału, a co za tym idzie – zniszczeniu elementu.
Opis podejścia symulacyjnego
W obecnych latach projektowanie elementów konstrukcyjnych wspomagane jest zazwyczaj wynikami symulacji numerycznych. Nie inaczej dzieje się w przypadku elementów z tworzyw termoplastycznych. Jak wynika z przedstawionych powyżej wyników pomiarów, w celu uzyskania poprawnych wyników analiz strukturalnych tych elementów konieczne jest uwzględnienie anizotropii ich własności mechanicznych. Najprostszy sposób polega na obniżeniu sztywności materiału podanej w jego karcie technicznej o zadaną wartość, przeważnie równą 20%-40%, wyznaczaną w oparciu o badania wytrzymałości wiosełek. Obniżenie to ma na celu pośrednie uwzględnienie zmiennej orientacji włókien we wtryskiwanym detalu, jednak nadal materiał w obliczeniach traktowany jest jako izotropowy, a więc posiada on takie same własności w całej objętości, bez względu na kierunki działających obciążeń. W przypadku projektowania elementów z materiałów termoplastycznych, oprócz typowych obliczeń strukturalnych wykonuje się także symulacje procesu wtryskiwania. Ich wyniki po- zwalają na sprawdzenie technologiczności zaprojektowanego elementu i optymalizację procesu jego wytwarzania. Dodatkowo mogą być pomocne w oszacowaniu anizotropowych własności mechanicznych końcowego produktu. Zaawansowane podejście symulacyjne do elementów wykonanychz kompozytów termoplastycznych polega na uwzględnieniu orientacji włókien w symulacjach strukturalnych detalu. W podejściu tym konieczne jest przeprowadzenie na wstępie symulacji procesu wtryskiwania analizowanego elementu. Do tego celu posłużono się oprogramowaniem Autodesk Moldflow Insight. Narzędzie to pozwala zamodelować proces wtryskiwania tworzyw sztucznych uwzględniając wszystkie fazy jego cyklu. Pozwala także na wyznaczenie orientacji włókien w analizowanym detalu, która to informacja jest następnie używana w analizach wytrzymałościowych przeprowadzonych w programie Abaqus. Transfer informacji o orientacji włókien do programu Abaqus realizowany jest pośrednio poprzez moduł oprogramowania Digimat, służącego do modelowania materiałów kompozytowych. Jako dane wejściowe w obliczeniach zadaje się tu własności niewypełnionego, bazowego materiału termoplastycznego oraz wypełnienia (włókien szklanych), a także ich udział, masowy bądź objętościowy, w stosowanym kompozycie. Następnie program poprzez proces homogenizacji wylicza własności mechaniczne wynikowego materiału. Dodatkowo, wykorzystywany moduł Digimat uwzględnia wartości tensora orientacji włókien z symulacji procesu wtryskiwania i wylicza zastępcze wartości materiałowe dla każdego elementu skończonego modelu numerycznego analizowanego komponentu, które to wartości użyte sąw obliczeniach strukturalnych programu Abaqus. Na rysunku 2 przedstawiony został schemat wykorzystywanego podejścia symulacyjnego.
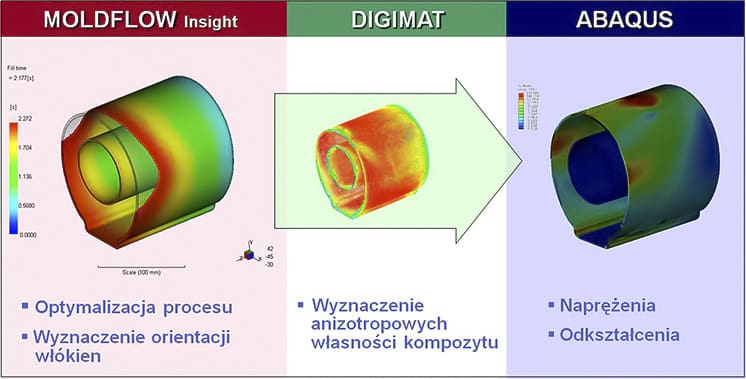
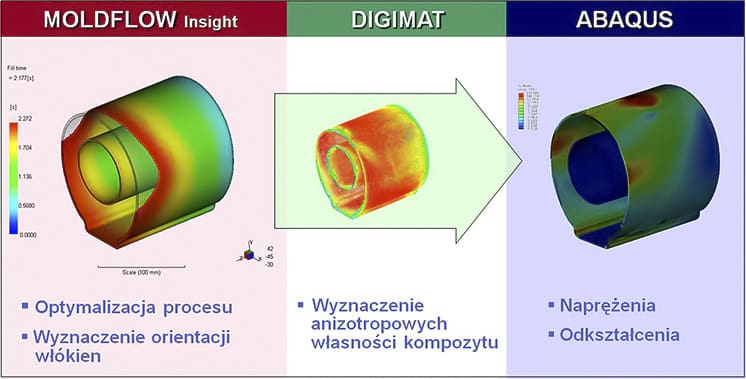
Weryfkacja podejścia symulacyjnego
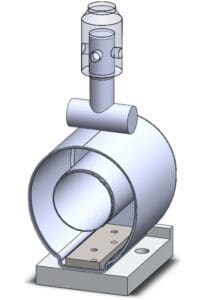
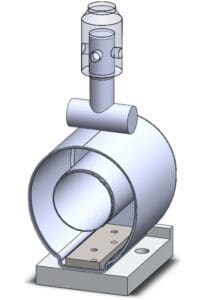
Przedstawione podejście symulacyjne weryfikowane było eksperymentalnie dla próbek wiosełkowych poddawanych próbie rozciągania. Zarówno dla wiosełek produkowanych bezpośrednio metodą wtryskiwania, według normy ISO 527, jak i wycinanych strumieniem wody z płytek kwadratowych uzyskano zadowalającą zbieżność wyników symulacji z rzeczywistością (błąd w najgorszym przypadku nie przekraczał 20%). Zastosowanie podejścia uproszczonego (materiał izotropowy o obniżonej sztywności) w przypadku wiosełek nie ma sensu, gdyż dostarczy poprawne wyniki tylko i wyłącznie w przypadku wiosełka wycinanego z płytki w kierunku orientacji włókien (przy założeniu obniżenia własności materiałowych o 20%). Dlatego, w celu zobrazowania korzyści płynących ze stosowania opisanego podejścia, posłużymy się wynikami uzyskanymi przy optymalizacji pojemnika ciśnieniowego wykonanego z materiału z grupy poliamidów, wypełnionego w 50% włóknem szklanym. Pojemnik o wymiarach gabarytowych 140 x 160 x 145 mm i średniej grubości ścianki 3 mm w docelowej aplikacji poddawany jestobciążeniu ciśnieniem zewnętrznym o wartości dochodzącej do 6 barów. Wytrzymałość kompletnego pojemnika (wraz z wieczkiem zamykającym) testowana była w zbiorniku olejowym, jednak metoda ta ogranicza się do stwierdzenia wartości granicznej ciśnienia, przy której pojemnik ulegał uszkodzeniu. W związku z tym, testy pojemnika prowadzone były również na maszynie wytrzymałościowej, gdzie w wersji otwartej poddawany był on działaniu siły ściskającej, przyłożonej w wybranym miejscu. Model pojemnika otwartego wraz z uchwytem i elementem przekazującym obciążenie przedstawione są na rysunku 3.
W pierwszym kroku przeprowadzono w pełni trójwymiarową symulację wtryskiwania z zastosowaniem 10 warstw elementów po grubości ścianki w celu precyzyjnego określenia orientacji włókien. Wynik orientacji włókien przedstawiono na rysunku 4, gdzie wartość liczbowa oznacza prawdopodobieństwo zorientowania włókien w kierunku płynięcia.
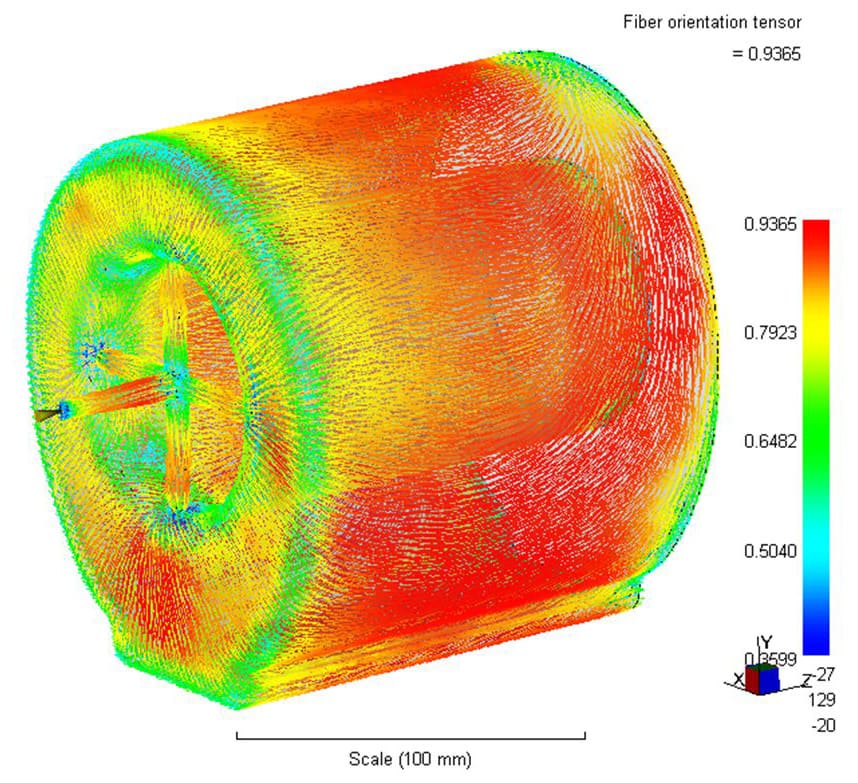
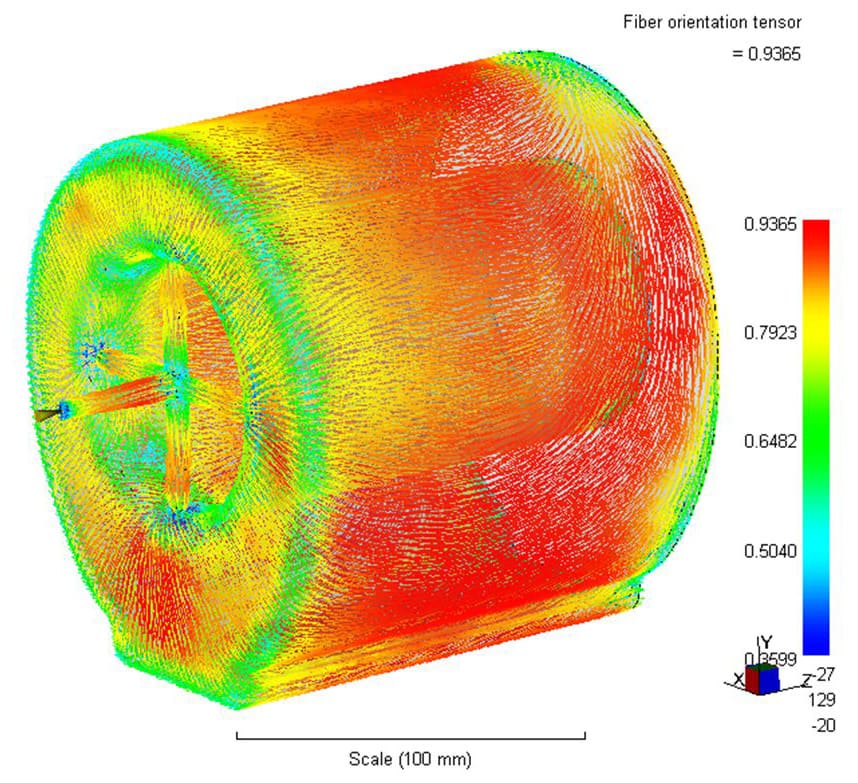
W kolejnym kroku przygotowano model numeryczny do przeprowadzenia analizy strukturalnej. Ponownie w celu właściwego odwzorowania orientacji włókien zdecydowano się na przygotowanie modelu o dziesięciu warstwach elementów po grubości ścianki z zastosowaniem elementów typu HEX, których liczba przekroczyła 500 000. W modelu numerycznym, przedstawionym na rysunku 5, element przekazujący obciążenie zamodelowano w formie sztywnej powierzchni cylindrycznej, a pojemnik utwierdzono na dwóch dolnych, płaskich powierzchniach. Wymuszenie, którego kierunek zaznaczony jest czerwoną strzałką, realizowano poprzez zadanie przemieszczenia. Następnie zdefiniowano własności materiału w programie Digimat (w wariancie idealnie sprężystym oraz sprężysto-plastycznym), zmapowano orientację włókien z siatki Moldflow do siatki Abaqus i przeprowadzono obliczenia.
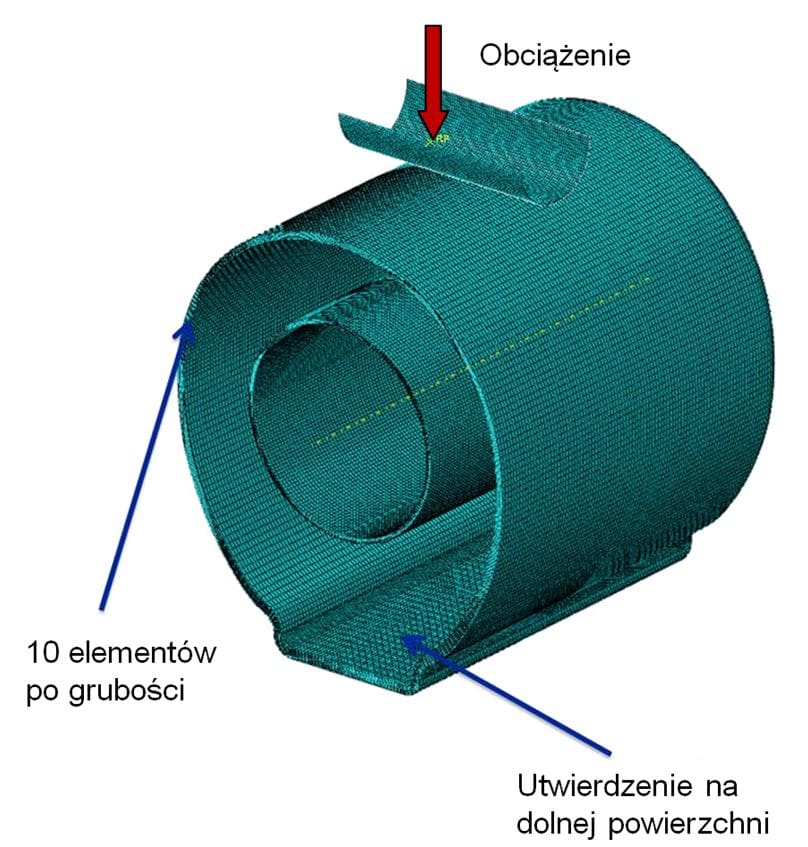
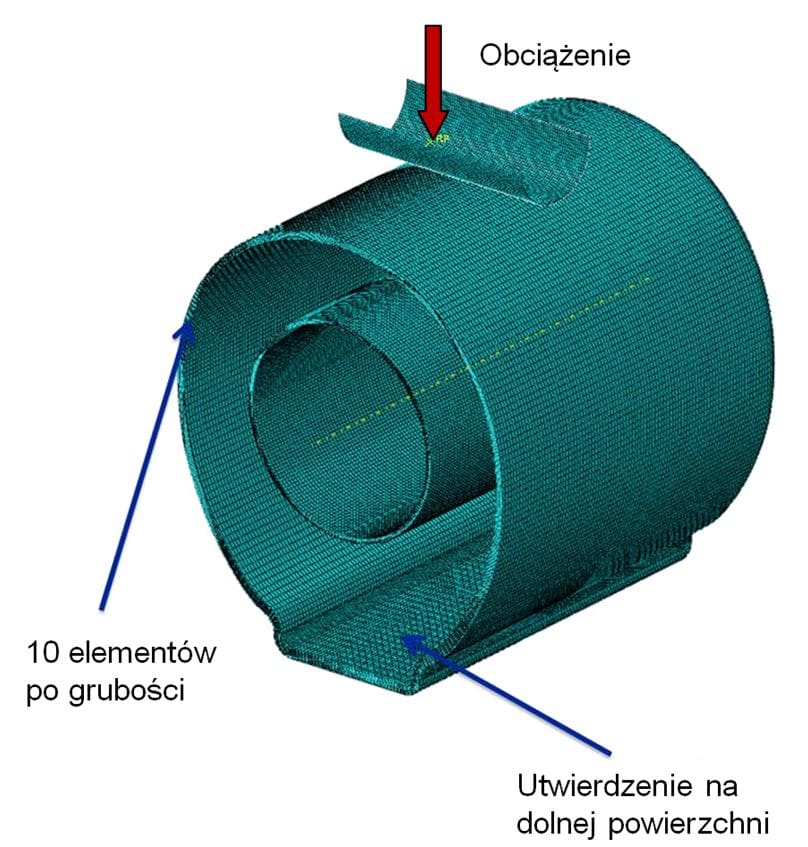
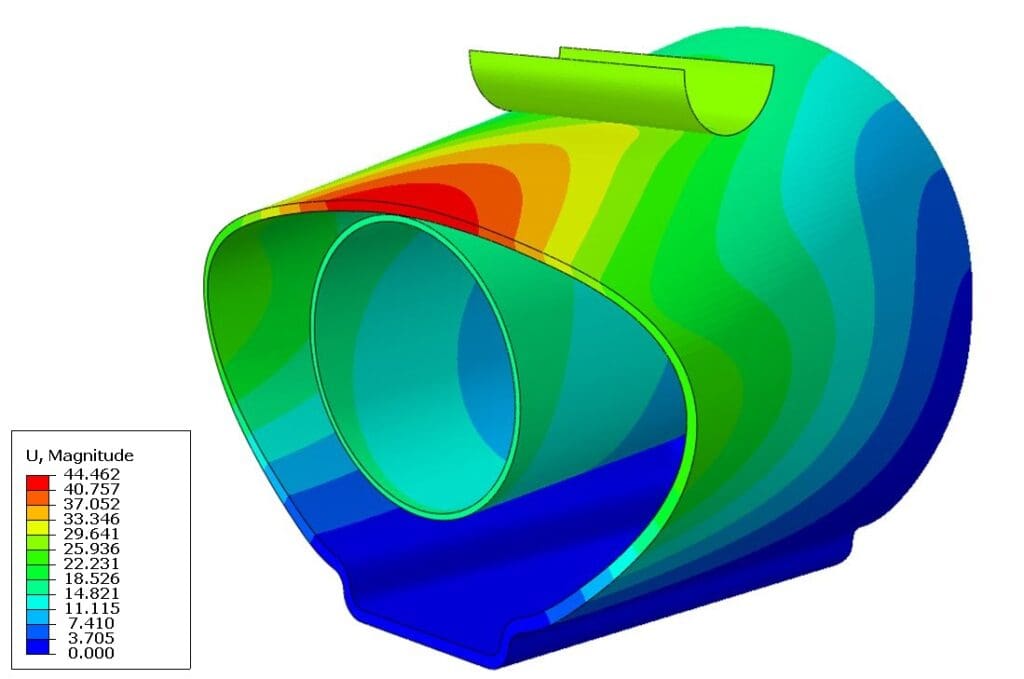
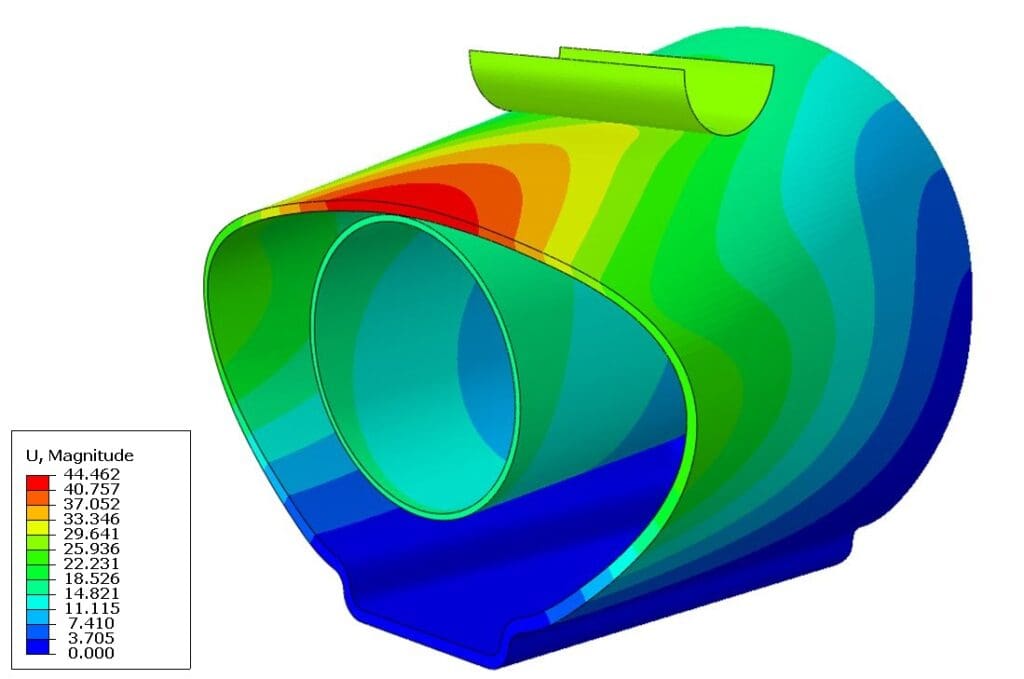
Wynik deformacji pojemnika w końcowej fazie obciążenia, dla podejścia uwzględniającego orientację włókien z zastosowaniem modelu materiału idealnie sprężystego, przedstawiono na rysunku 6.
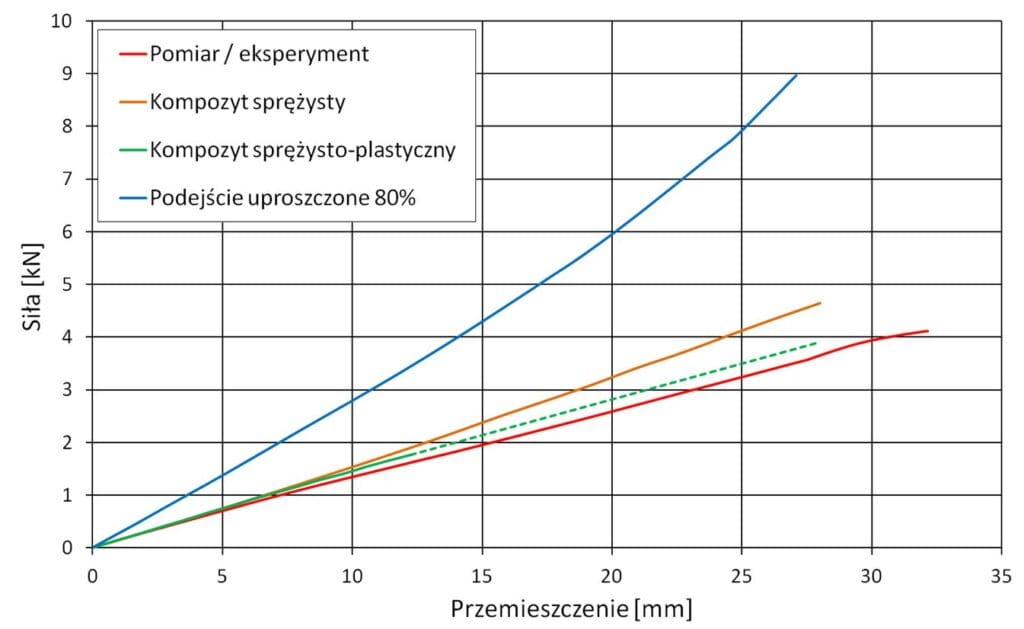
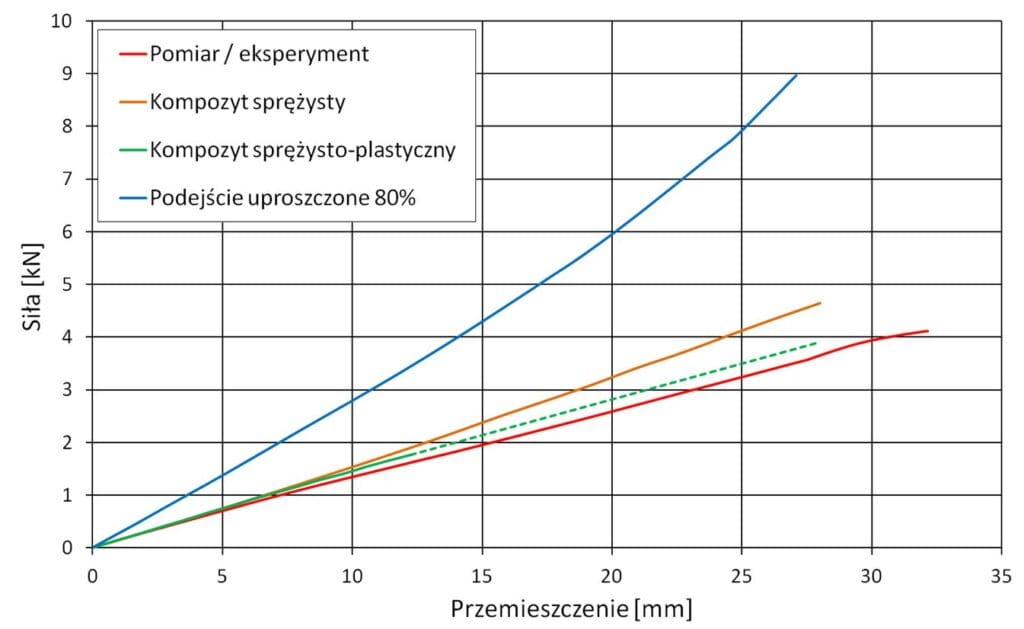
Na rysunku 7 przedstawiono wykresy wartości siły względem przemieszczenia uzyskane w eksperymencie oraz w symulacji, dla różnych własności materiałowych. Kolorem czerwonym zaznaczona jest krzywa, uzyskana z sześciu uśrednionych pomiarów na maszynie wytrzymałościowej, przy czym należy wspomnieć o wysokiej powtarzalności wyników (odchylenie standardowe 0,04 kN dla siły i 0,24 mm dla przemieszczenia). Kolorem pomarańczowym zaznaczono wyniki uzyskane z zastosowaniem opisywanego podejścia w wariancie z materiałem idealnie sprężystym. Jak widać sztywność pojemnika jest większa od rzeczywistej, co w końcowej fazie obciążenia skutkuje rozbieżnością do 30% względem eksperymentu. W przypadku zmiany modelu materiałowego na sprężysto-plastyczny uzyskano poprawę wyników (krzywa w kolorze zielonym), jednak zwiększono wyraźnie czas obliczeń, co w efekcie nie pozwoliło na ich ukończenie (przerywana część krzywej jest liniową ekstrapolacją wyników). Należy zwrócić szczególną uwagę na wyniki dla podejścia uproszczonego (materiał izotropowy z obniżonymi własnościami materiałowymi o 20%), przedstawione krzywą niebieską, gdzie sztywność pojemnika jest w znacznym stopniu przeszacowana. Analiza wyników uzyskanych w symulacji z wykorzystaniem uproszczonego podejścia nieuchronnie prowadzi do błędnych wniosków – wyznaczona w ten sposób wytrzymałość pudełka jest ponad dwukrotnie większa od wartości rzeczywistej.
Podsumowanie
Przedstawione podejście symulacyjne dla detali wykonanych z kompozytów termoplastycznych pozwala na uwzględnienie anizotropii materiału, a co za tym idzie uzyskanie wyników znacznie bliższych rzeczywistości niż w przypadku użycia modelu materiału izotropowego o zmniejszonej sztywności. Zaprezentowany przykład pojemnika ciśnieniowego pokazuje, iż dla elementów o złożonej geometrii podejście uproszczone może spowodować przeszacowanie ich nośności. Można oczywiście rozważyć dalsze obniżenie własności materiałowych w podejściu uproszczonym, aż do wartości równych własnościom kompozytuw poprzek włókna, jednak takie dane są z reguły niedostępne i w dodatku mogłoby to prowadzić do znacznego przewymiarowania detalu. Prezentowane podejście jest dość skomplikowane, wymaga zastosowania trzech komercyjnych pakietów oprogramowania oraz jest zdecydowanie bardziej czasochłonne w przygotowaniu modeli jak i przeprowadzeniu obliczeń. Należy jednak podkreślić, że optymalizacja detalu wykonanego z kompozytu termoplastycznego jest możliwa jedynie przy jego modelowaniu numerycznym, z uwzględnieniem informacji o orientacji włókien i ich wpływie na własności materiału.
Dariusz Bednarowski
Łukasz Malinowski
ABB Sp. z o.o.
Korporacyjne Centrum Badawcze, Kraków
Literatura:
Osswald T.A., Turng T., Gramann P.J. (edytorzy): Injection Molding Handbook; Hanser Publishers, Monachium 2002
Fischer J.M.: Handbook of molded part shrinkage and warpage; Plastics Design Library, Nowy Jork 2003
Bednarowski D., Malinowski Ł., Laskoś P.: Modeling of reinforced TPs’ mechanical performance with use of failure indicators; Proceedings of the Digimat Users’ Meeting, Luksemburg 2010
Van Meulebeke G., Blairon J-M, Hazard L.: On the identifcation of the parameters required to describe and to predict the elastoplastic behaviour of a composite made of short glass fbers; Proceedings of the Digimat Users’ Meeting, Bruksela 2008
Bednarowski D., Malinowski Ł., Mueller R. E.: Kompleksowa analiza wytrzymałościowa detali z tworzyw sztucznych wypełnionych krótkim włóknem; Tworzywa Sztuczne i Chemia Nr 6/2005, str. 26-28
Norma ISO 527: Plastics – Determination of tensile properties
artykuł pochodzi z wydania 12 (51) Grudzień 2011